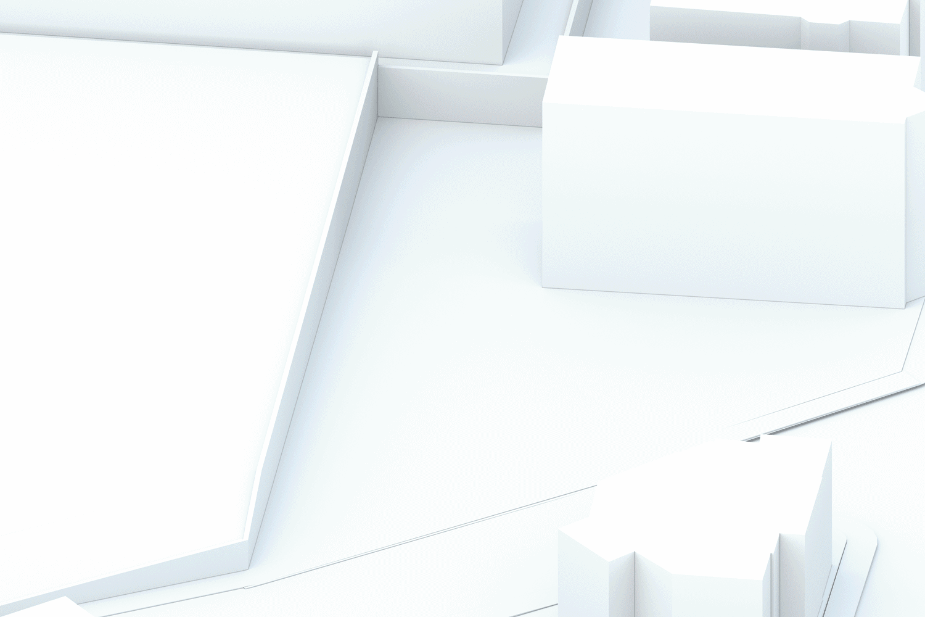
Model-C
CATEGORY: Architecture (Professional)
LOCATION: Boston, MA
TYPE: Residential/Commercial
PROGRAM: 15 units; Co-Working
HEIGHT: 5 stories; 58 feet
AREA: 20,000 sf
FIRM: Generate
TEAM: Placetailor (Developer, GC, AOR); BuroHappold (Structure); Ripcord Engineering (MEP); Code Red (Code)
PHASES: Schematic Design, Design Development
DURATION: 2 months
STATUS: Permit Review
DESCRIPTION:
Set to become Boston’s first-ever full Cross-Laminated-Timber (CLT) Passive House demonstration project, Model-C aims to serve as a catalyst for other communities across the region— and more generally across North America— to more effectively help address the increasing shortage of affordable housing while also tackling the pressing challenges of climate change.
Comprised of 14-residential units and a pilot affordable co-working space on the ground floor for local community members, the new and innovative five-story 20,000 square foot mixed-use building utilizes a prefabricated modular and replicable “kit of parts” construction system for developing healthy, comfortable, and carbon conscious workforce housing in the Lower Roxbury area of South Boston.
By replacing conventional concrete and steel construction materials— which significantly contribute to the release of carbon dioxide into the atmosphere— the Model-C system instead has the potential to act as a carbon sink by storing atmospheric carbon in the all-timber structure over the lifetime of the building.
Intended to meet Passive House certification and be built to the new Boston Department of Neighborhood Development “Zero Emissions Standards,” Model-C will aim to operate at a “net-zero carbon” and “net-zero energy” level by generating more power than the buildings uses via its extensive solar roof canopy.
The project is set to begin construction in the fall of 2021.
ROLE/CREDITS:
As the Director of Architecture at Generate, I led the design of the building layouts including the ground and residential floors, dwelling units, CLT system detailing, and overall project coordination with our consultants and collaborators at Placetailor. Along with Generate’s Director of Design, I also worked closely on the building’s formal massing articulations and exterior facade design. The presentation drawings below were finalized by interns, the image renderings are by Forbes Massie, and the assembly animation was completed by the Director of Design.
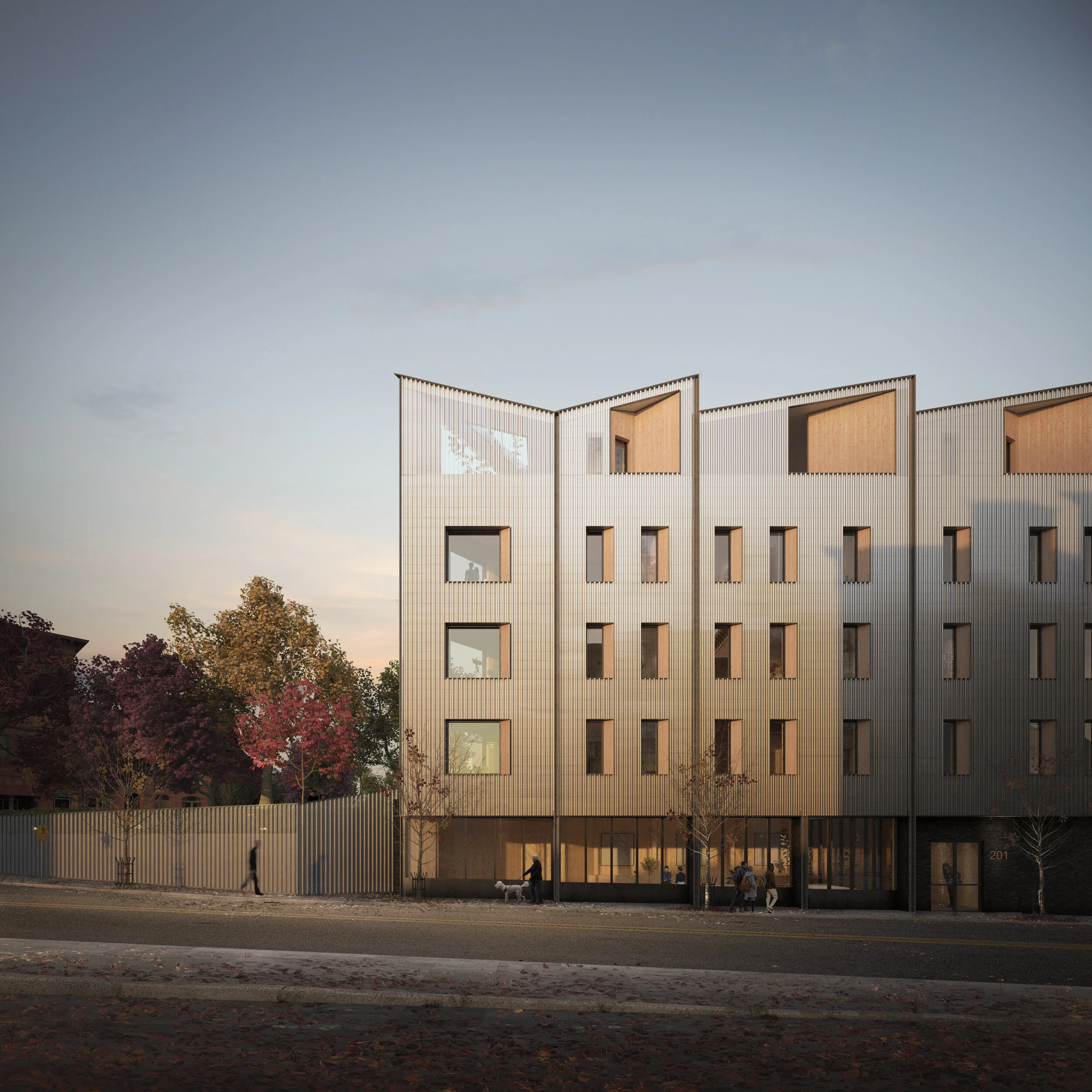
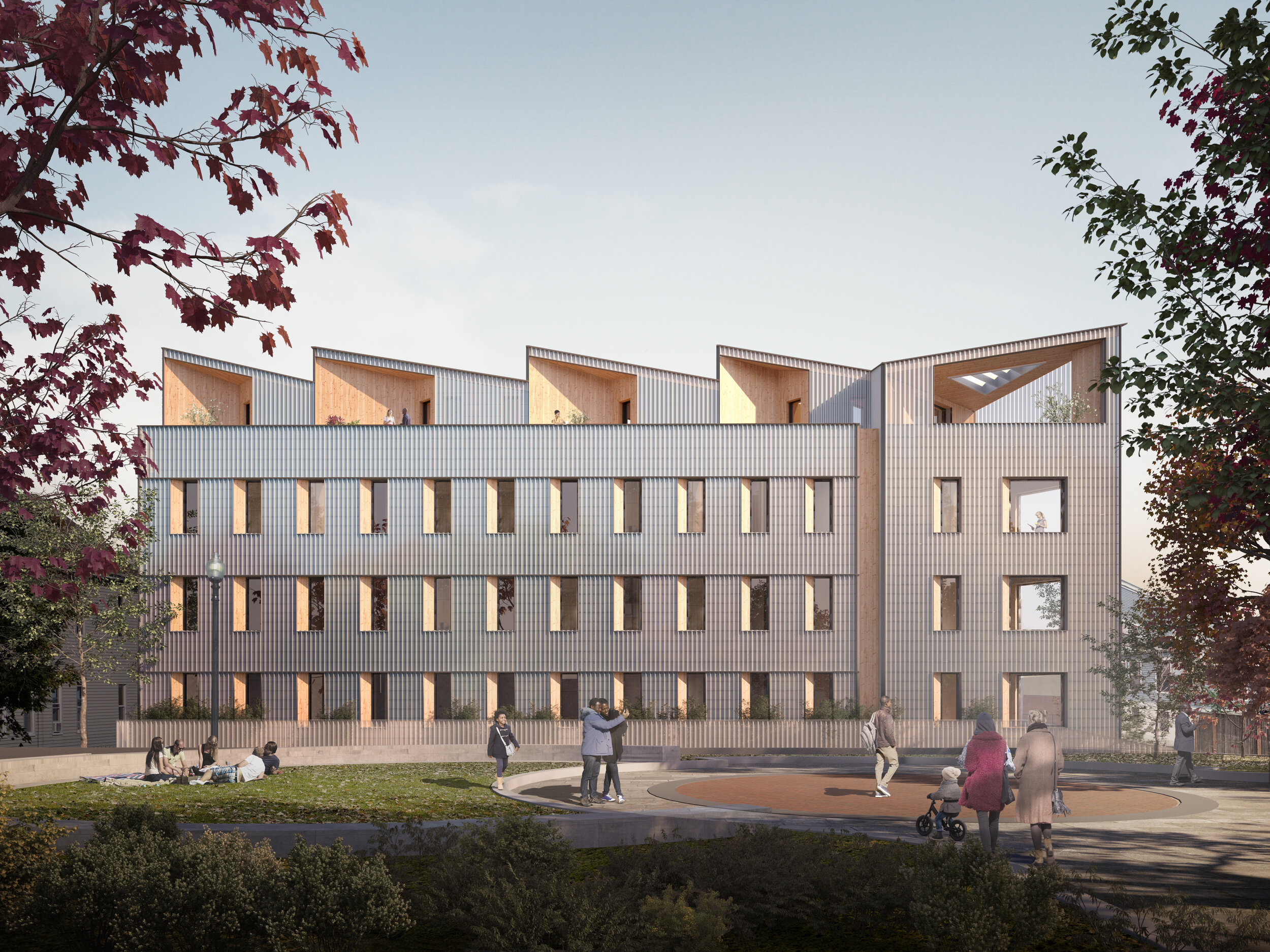
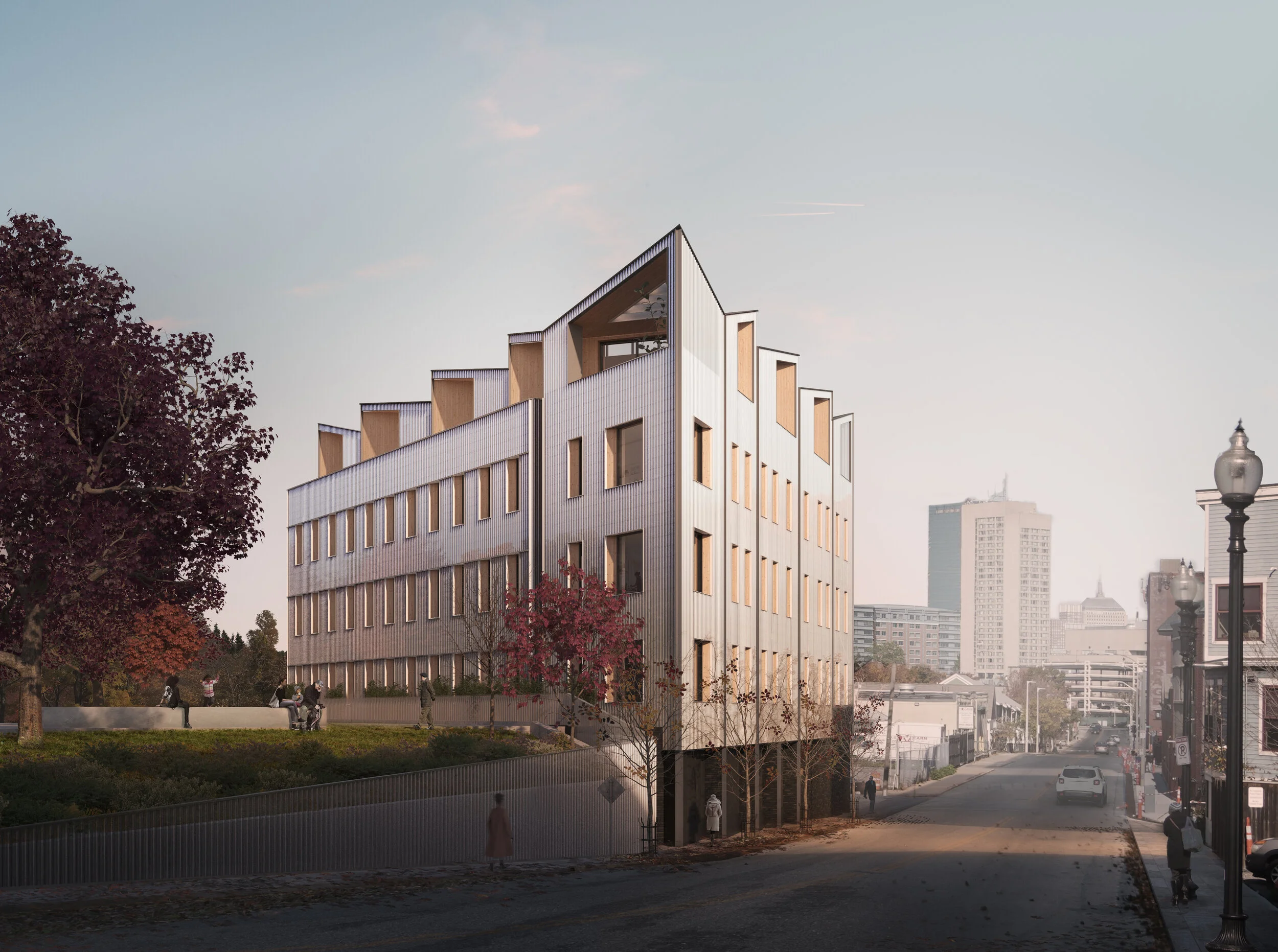
Row Home Redefined
Located at the intersection of an industrial and residential zone, Model-C takes inspiration from Boston’s unique residential character by mimicking the repetition and rhythm of the neighboring row houses along its main street edge while also reflecting the nearby industrial area through the use of a translucent metal paneling system along the building’s exterior facade.
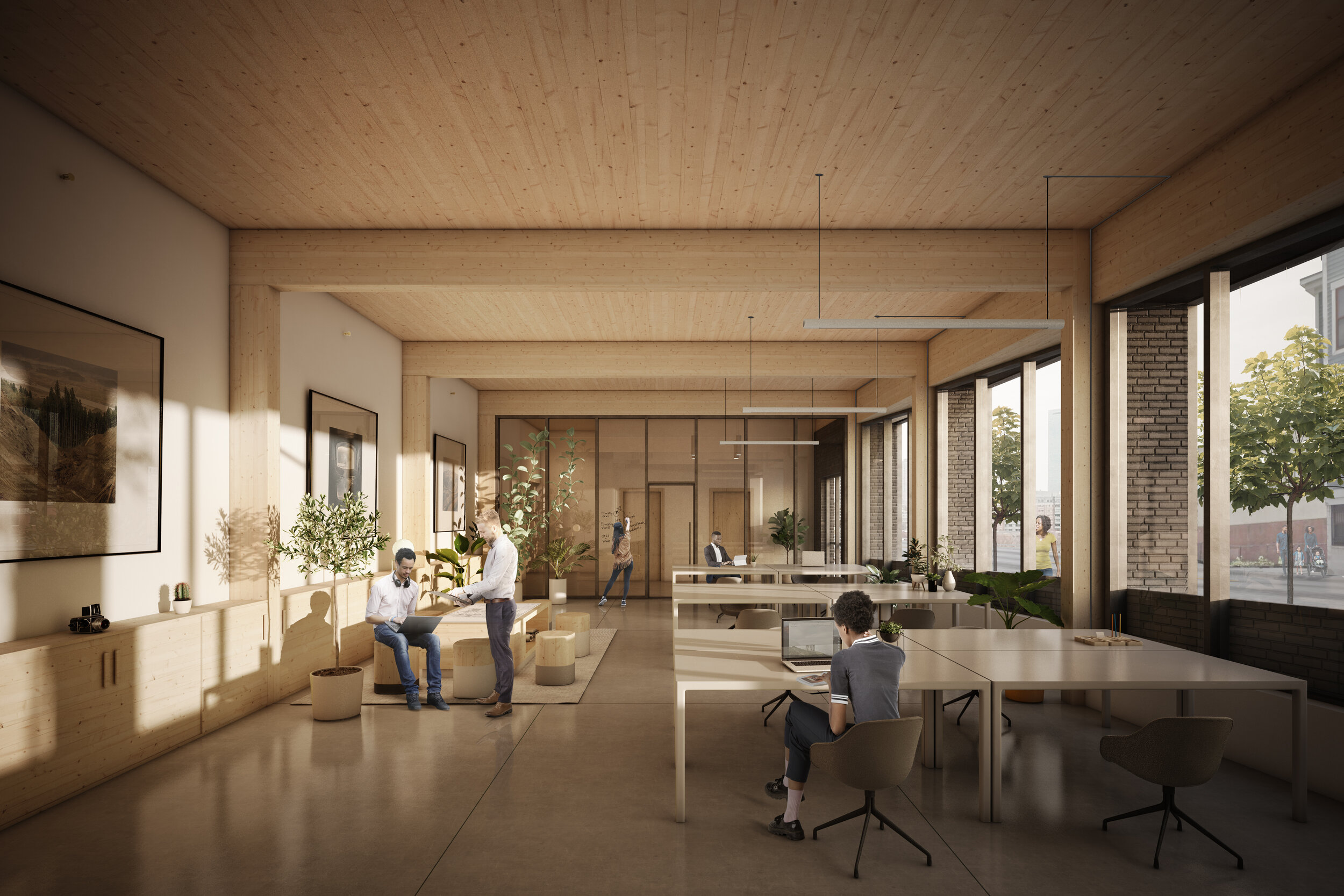
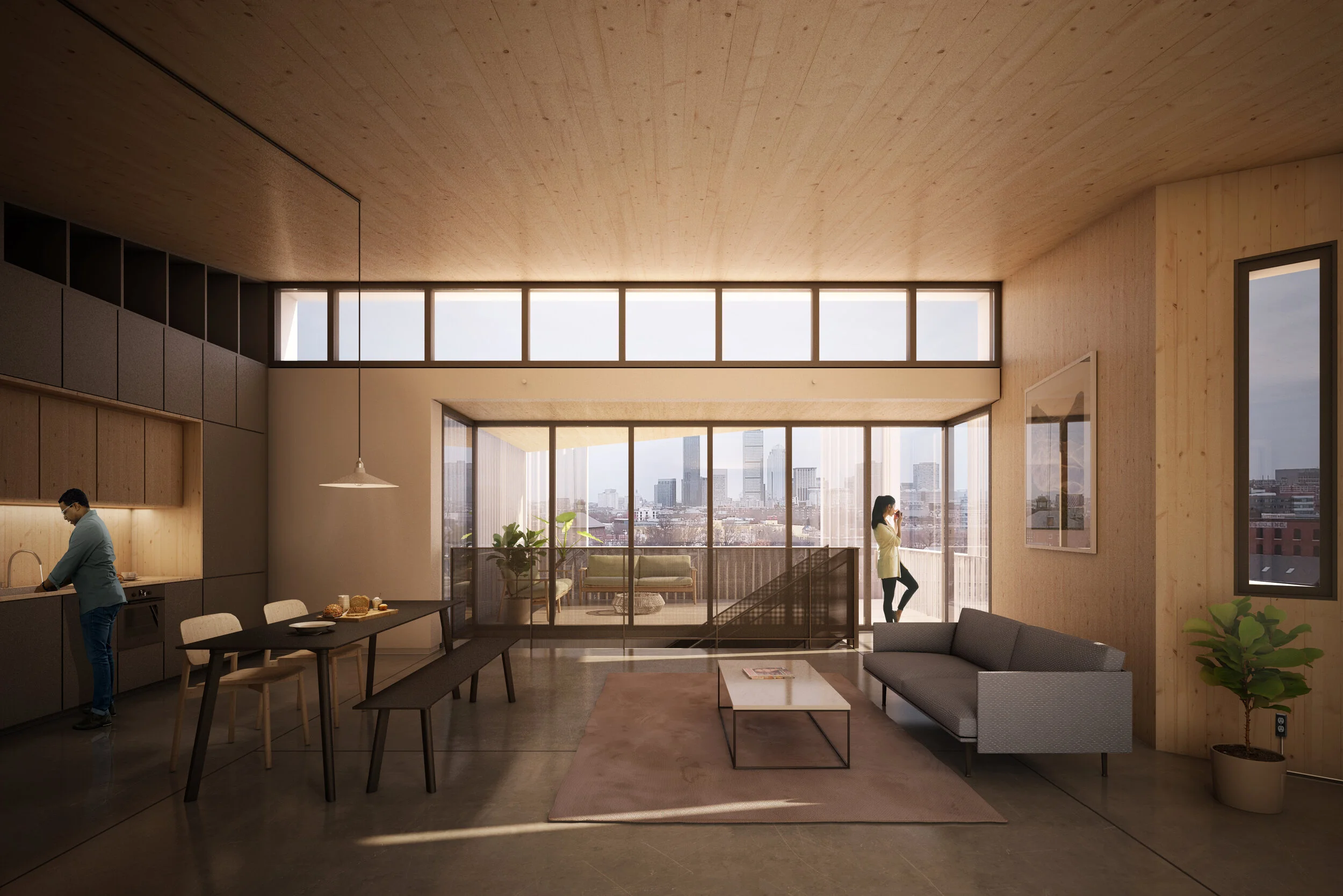
Improved Indoor Environment
By exposing CLT on interior wall and ceiling surfaces, the need for drywall is eliminated reducing overall construction time and costs while also improving indoor air quality by reducing potentially toxic paints and chemicals used in conventional interior fit outs. Wood’s unique biophilic, thermal, acoustic, and hygroscopic qualities also add to the comfort of interior spaces by providing improved occupant health, wellness, and productivity.

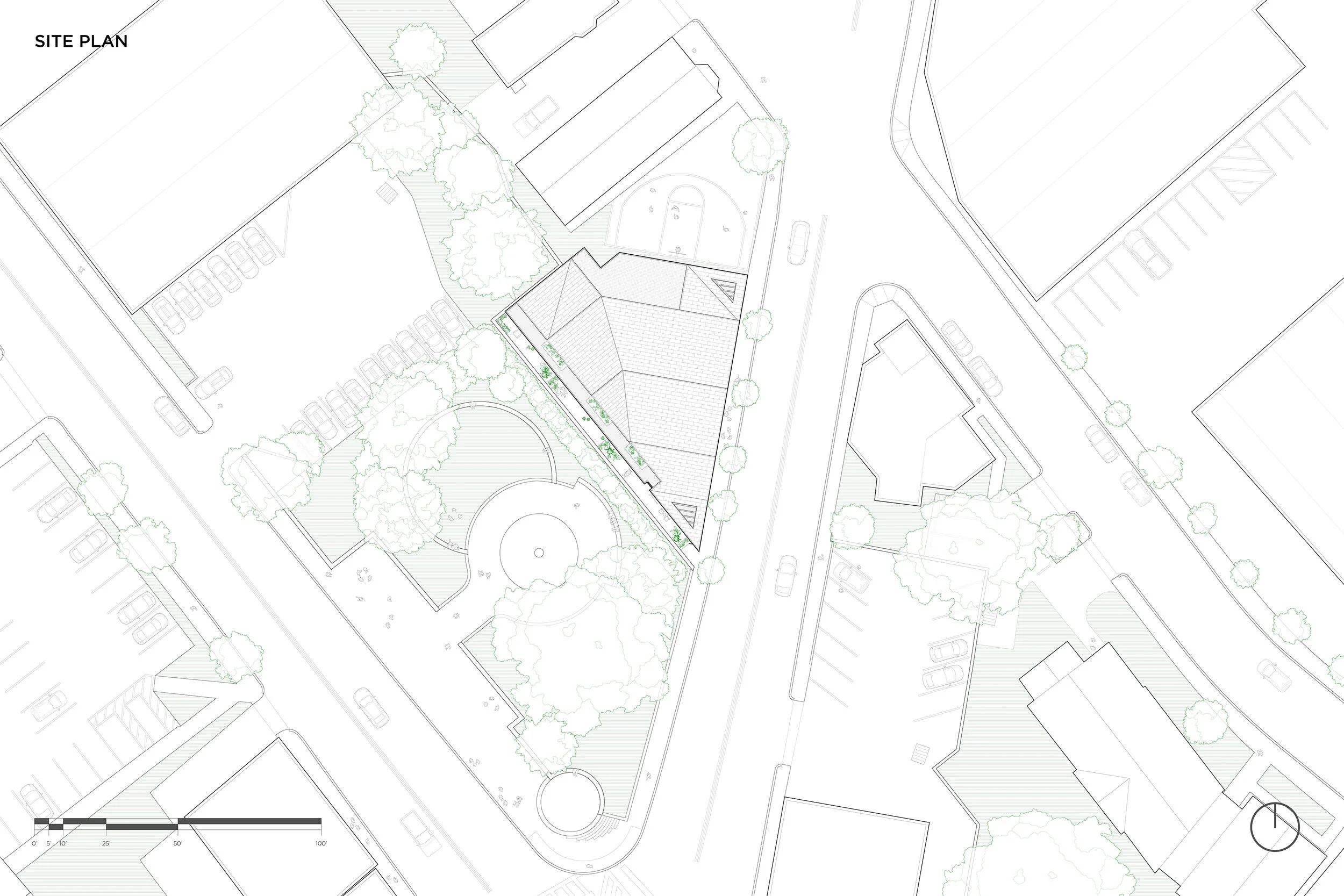
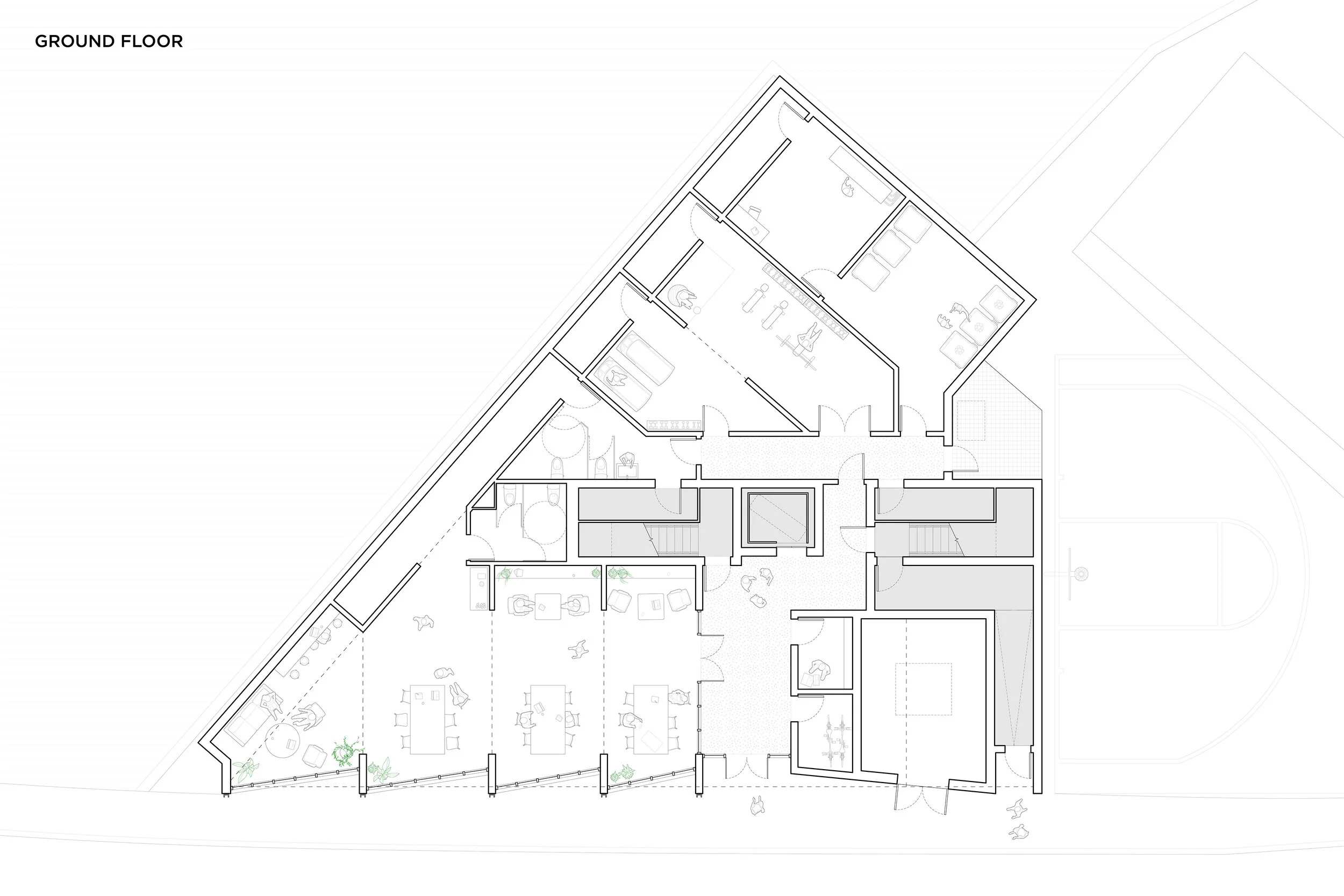
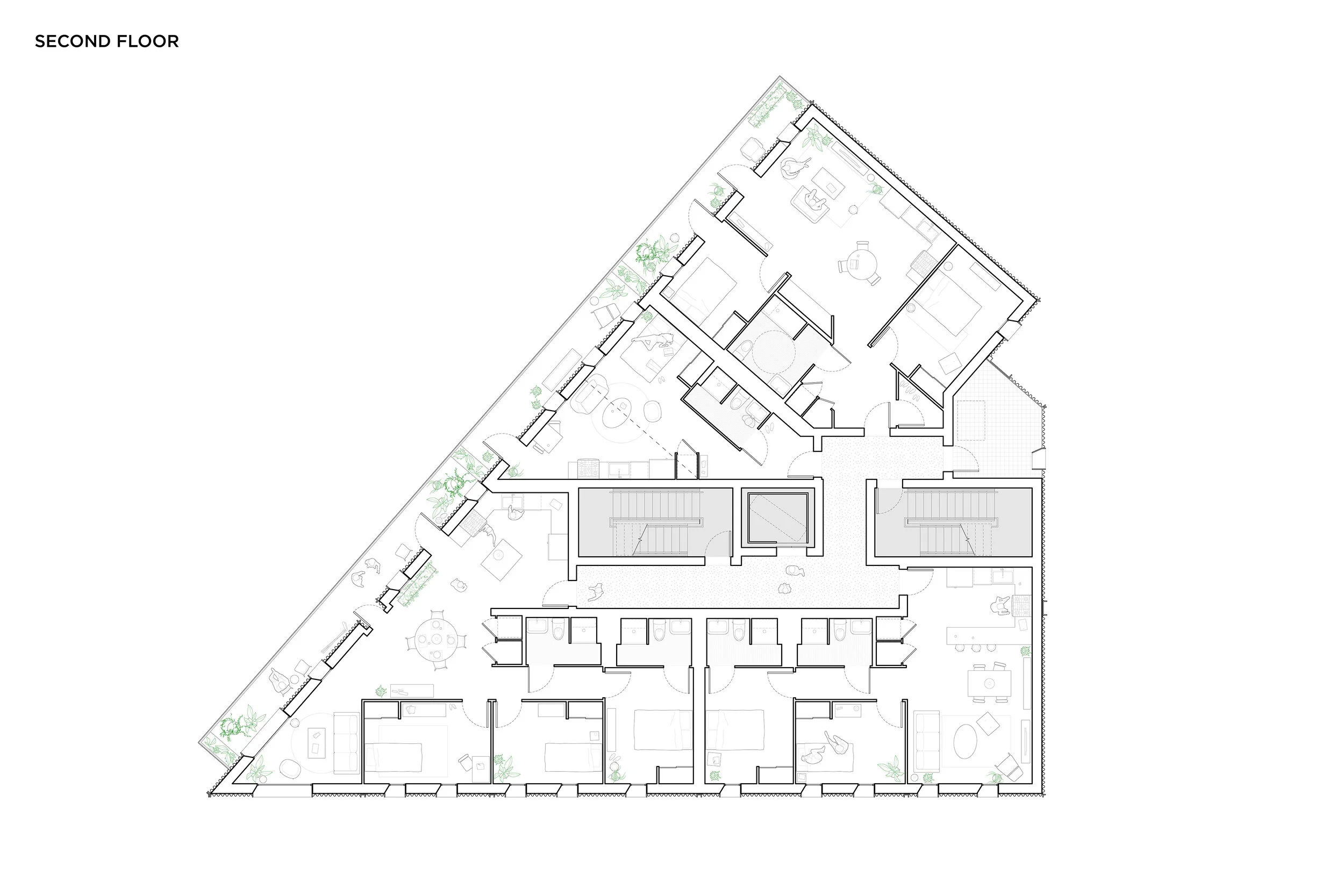


System Flexibility
The tight triangular site demonstrates the ability of the system to flex to unique site and programmatic conditions. CLT walls here not only function as the building’s structure but also as its interior space planning system significantly reducing or completely eliminating conventional interior framing while strategically located glulam beams enable larger floor areas such as the ground floor co-working spaces and the rooftop penthouses.
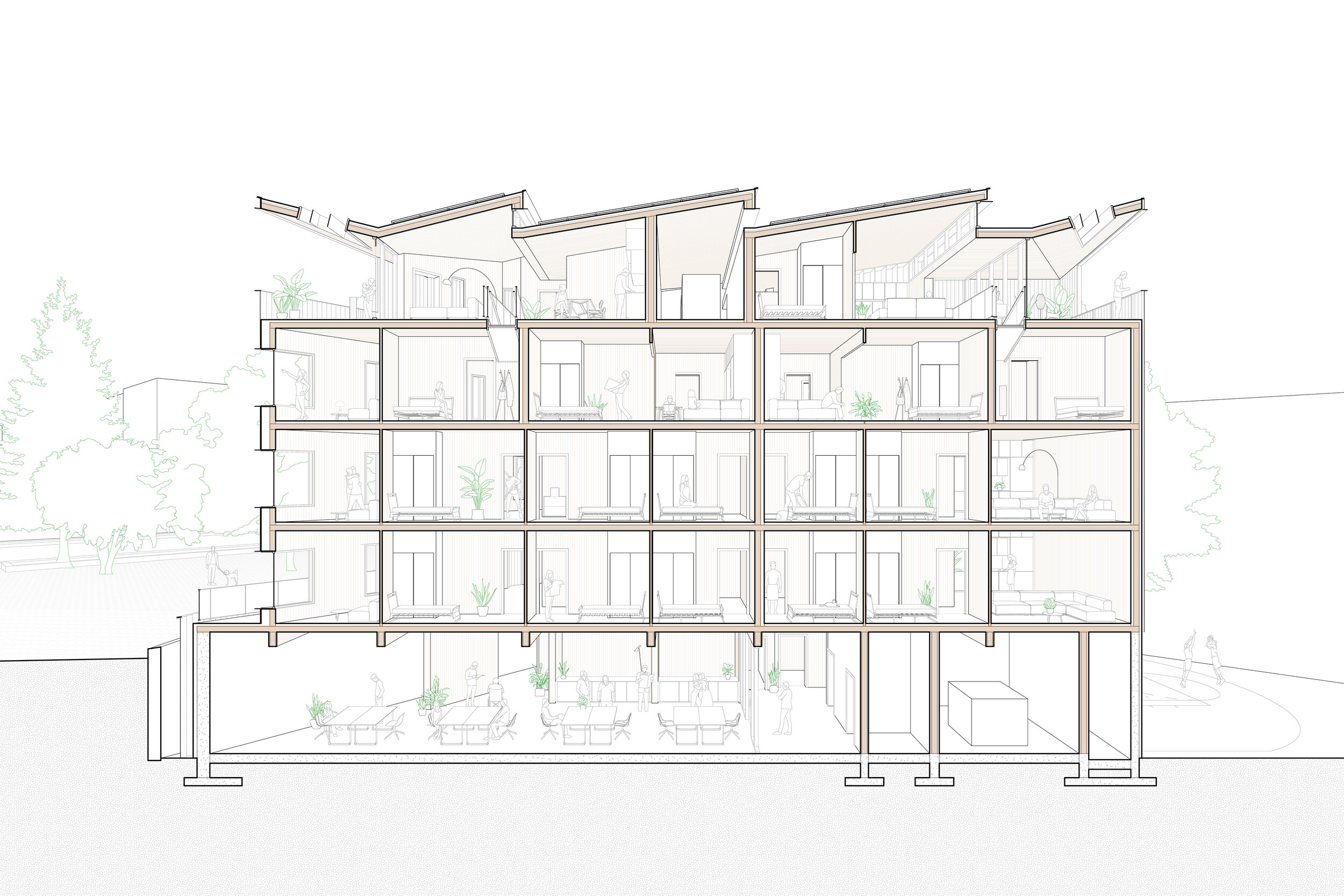

Assembly <> Disassembly
The “kit-of-parts” structural system— along with modular bathroom pods that are prefabricated off-site and that can be hoisted and easily plugged into the building— enables not only rapid assembly to save construction time and cost but also disassembly and reuse of materials at the end of the Model-C’s useful life in order to reduce waste and improve overall resource productivity.